Cleanroom Construction Regulations and Navigating Compliance Standards
- zachsievert15
- May 28, 2024
- 2 min read
Cleanroom construction is a highly specialized field that demands strict adherence to regulatory standards to ensure optimal contamination control and safety. Navigating these compliance standards can be complex, but it is crucial for maintaining the integrity and functionality of cleanrooms. Key regulations include ISO 14644, which provides a framework for air cleanliness classification, and the FDA's Current Good Manufacturing Practice (CGMP) guidelines, essential for the pharmaceutical and biotech industries.
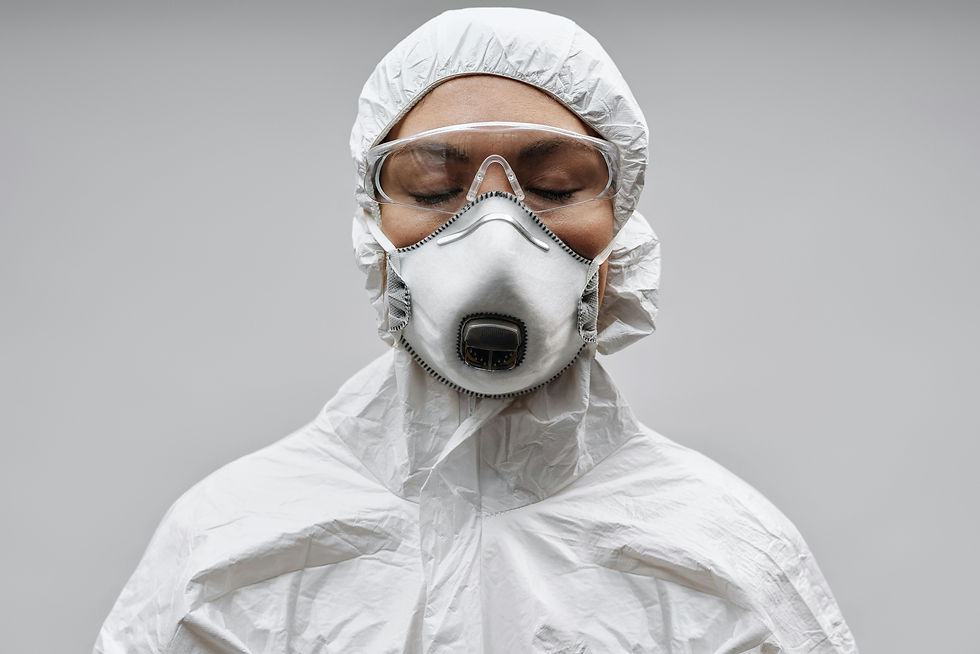
ISO 14644 serves as the cornerstone for cleanroom classification. It outlines the permissible limits for airborne particulate matter and details the testing procedures required to meet these standards. Understanding the particle count limits and regularly conducting these tests are essential steps in achieving and maintaining the desired cleanroom class. Compliance with ISO 14644 ensures that the cleanroom environment is controlled to prevent contamination, crucial in industries where even the smallest particles can compromise product quality.
The FDA's CGMP guidelines emphasize the importance of design, monitoring, and control of manufacturing processes to ensure product quality and safety within cleanrooms. These guidelines cover various aspects, including facility design, equipment maintenance, and procedural controls, to minimize contamination risks. CGMP compliance ensures that products are consistently produced and controlled according to quality standards, vital for protecting consumer health.
To ensure compliance, engage with experts in cleanroom design and construction familiar with these regulatory requirements. A skilled cleanroom builder or cleanroom engineer can guide you through the intricacies of cleanroom construction. Their expertise can help create a facility meeting all necessary standards. Additionally, ongoing staff training on compliance procedures and regular monitoring of the cleanroom environment are vital to maintaining standards. Training ensures personnel understand contamination control's importance and are equipped to maintain cleanroom integrity.
Implementing a reliable quality management system (QMS) is another essential component of regulatory compliance within cleanroom facilities. A QMS helps systematically manage processes, ensuring all regulatory requirements are consistently met. It facilitates continuous improvement, crucial in adapting to regulatory changes. A well-implemented QMS supports maintaining high standards and promotes a culture of quality within the organization.
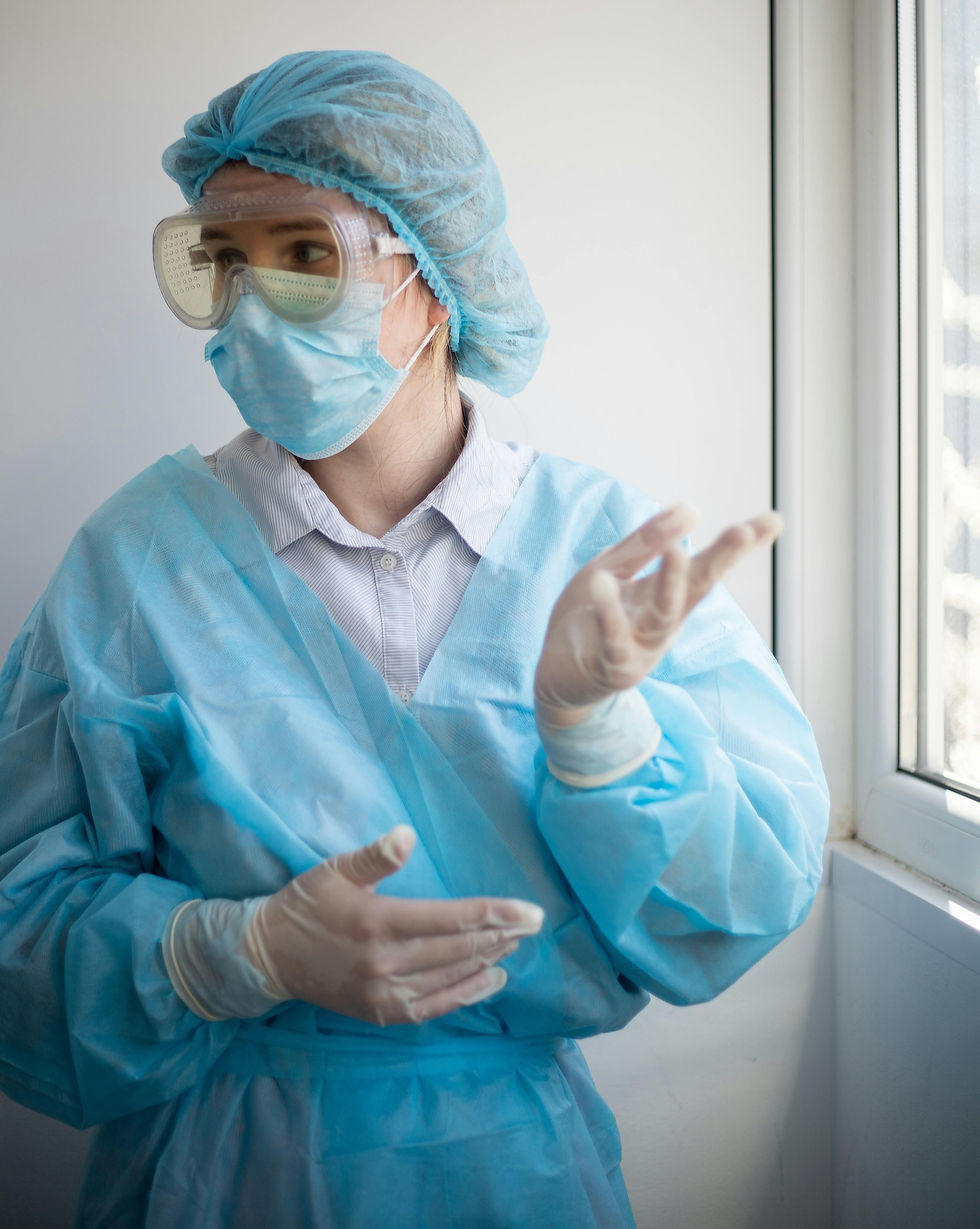
While navigating cleanroom construction regulations is challenging, staying informed and proactive is key. By understanding and adhering to ISO 14644 and FDA CGMP guidelines, engaging with knowledgeable cleanroom experts, and maintaining rigorous quality management practices, you can ensure your cleanroom meets all necessary regulatory standards and functions optimally.
For expert guidance in navigating cleanroom construction regulations and ensuring compliance with stringent standards, consider partnering with Designtek Consulting. Our experienced team specializes in cleanroom design and construction, prioritizing safety, reliability, and compliance. Learn more about our services at Designtek Consulting and take the first step toward achieving optimal cleanroom performance and regulatory adherence.
Commentaires