Construction Management Tips for Cleanroom Success
- zachsievert15
- 15 minutes ago
- 6 min read
Designing and building a cleanroom is never a one-size-fits-all project. From highly specialized environments in pharmaceutical production to microelectronics and medical device manufacturing, cleanrooms are precision spaces. That’s why proper construction management is essential to ensuring success—not only in meeting stringent requirements but also in staying on schedule and within budget. Whether you're building your first cleanroom or upgrading an existing space, a thoughtful, organized approach makes all the difference.
This article explores practical and proven construction management tips that contribute to cleanroom success, helping you avoid costly delays and ensure compliance every step of the way.
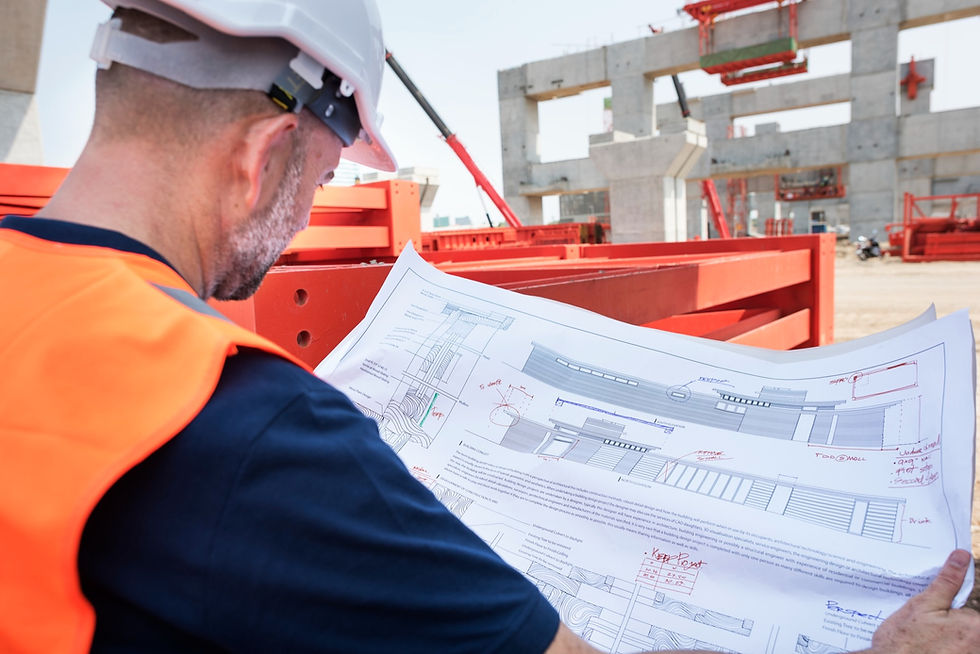
Understanding the Unique Challenges of Cleanroom Construction
Building a cleanroom isn’t like constructing a typical commercial facility. Every decision—from layout and materials to HVAC system design and airflow management—has to align with strict cleanliness and contamination control standards.
Here are a few key challenges unique to cleanroom construction:
Precise control over airflow and pressure differentials
Selection of non-shedding, easy-to-clean materials
Integration of complex cleanroom HVAC systems
Cleanroom classification compliance (ISO, GMP, etc.)
Coordination between design, engineering, and trades
Unlike traditional building projects, cleanroom construction often requires higher tolerances and unique certifications, making the role of cleanroom engineering and experienced contractors absolutely vital. With so many moving parts, cleanroom construction management demands a high level of coordination, specialized knowledge, and close attention to detail.
Start with Clear Project Goals and Requirements
Before breaking ground, you need to understand exactly what your cleanroom must achieve. Are you targeting ISO Class 7? Will your processes require humidity control or specific temperature ranges? Will hazardous materials or biohazards be handled?
Defining your cleanroom’s purpose and classification guides every design and construction decision. For example, pharmaceutical clean rooms may require specific finishes, gowning procedures, and air change rates, while electronics manufacturing cleanrooms might prioritize static control and laminar flow.
Involving a knowledgeable cleanroom builder early in the planning process ensures your team designs around regulatory requirements rather than having to retrofit solutions later. A detailed project scope—supported by cleanroom engineering professionals—sets the tone for efficient construction management and minimizes miscommunication.
Construction Management Tips for a Successful Build
Cleanroom projects have little room for error, which is why applying focused construction management tips can greatly increase your project’s likelihood of success. These tips include aligning design with regulatory standards, selecting the right cleanroom contractor, and engaging HVAC specialists early in the process. Effective construction management doesn’t just keep the timeline on track—it helps prevent costly missteps and improves long-term cleanroom performance.
Teams that incorporate these strategies tend to encounter fewer surprises along the way. Cleanroom construction management is not just about logistics; it’s about ensuring every layer of the build—from structural to environmental systems—is aligned with compliance and performance goals.
Choose the Right Team for the Job
Cleanroom construction is a specialized niche. The architect who designed your office building may not understand laminar flow dynamics or the nuances of cleanroom HVAC.
Your ideal project team should include:
A cleanroom contractor with hands-on experience
Cleanroom design and engineering professionals
Mechanical experts familiar with cleanroom HVAC systems
General contractors who can coordinate across disciplines
Having a cleanroom construction management team that understands both the science and the logistics of cleanroom construction helps reduce the risk of missteps during the build. Teams like DesignTek Consulting are equipped to manage the demands of custom-built clean rooms, offering both cleanroom design and end-to-end project coordination that streamline the process from start to finish.
Emphasize Communication and Collaboration
Strong communication between stakeholders is the foundation of any well-managed construction project—especially one involving clean rooms.
Establish clear points of contact for each phase of the project. Set up regular meetings to review progress, resolve issues, and confirm next steps. Encourage open dialogue among contractors, engineers, and facility managers to keep everyone aligned on the technical requirements.
Using project management software or shared dashboards can streamline this collaboration and keep updates transparent and accessible. Cleanroom construction projects often involve multiple trades and sequential scheduling. Miscommunication can lead to delays, rework, and budget overruns—something easily avoided with proactive planning and daily check-ins.

Plan for Air Filtration and HVAC Early
One of the most critical elements of any cleanroom is its HVAC system. Air filtration systems, pressure controls, and ductwork design all directly affect the room's classification and performance.
A common mistake is waiting too long to engage HVAC specialists, resulting in design limitations or space constraints that impact performance. Early coordination ensures your HVAC system will:
Maintain cleanroom classification
Provide required air change rates
Handle temperature and humidity control
Support pressure differentials between clean zones
Cleanroom HVAC systems must also be designed to maintain cleanliness standards over time. This includes the use of HEPA or ULPA filters, pressure monitoring systems, and controls that maintain strict environmental parameters. These systems require regular maintenance and testing to continue functioning properly, so accessibility and reliability should be considered in the initial construction phase.
Cleanroom HVAC is a foundational part of the facility and must be treated with the same importance as structural or electrical elements.
Coordinate Construction Around Contamination Control
Unlike traditional construction, building a cleanroom means working with contamination control top of mind—sometimes even while the surrounding facility is operational.
Some construction management tips for cleanliness include:
Segregating cleanroom construction areas from general work zones
Using HEPA-filtered vacuums and protective coverings
Training workers on cleanroom protocols
Cleaning tools and materials before entry
Phased commissioning to validate each section as it's completed
Cleanroom contractors should work closely with project managers to ensure every worker on-site understands how their tasks impact the overall cleanliness of the project. Even small oversights—such as bringing in unclean tools or using inappropriate materials—can compromise progress and delay certification.
Plan for Cleanroom Validation and Certification
Every cleanroom project ends with a critical phase: validation. This process confirms the cleanroom meets design specifications and regulatory requirements for particle counts, pressure, and airflow.
To prepare for validation:
Ensure documentation is updated throughout the build
Review cleanroom construction materials and methods
Schedule environmental testing (e.g., particle counts, airflow visualization)
Coordinate third-party certification if needed
Construction management teams should plan for validation well in advance. This includes setting aside time for airflow testing, filter integrity testing, and cleanroom classification assessments. Rushing or skipping validation jeopardizes compliance and delays operations. Cleanroom construction management strategies should also account for re-testing if any issues are found during the initial validation.
Address Utilities and Wastewater Management
Utilities such as power, compressed air, and data cabling need to be integrated seamlessly. Equally important is wastewater management—especially for cleanrooms handling chemicals, solvents, or biologics.
Designing systems for safe discharge and filtration isn’t just a regulatory requirement—it’s part of ensuring operational efficiency and minimizing environmental impact. Proper wastewater management also plays a role in cleanroom certification, as untreated or improperly managed waste can pose serious contamination risks.
Consider future expansion needs as well to avoid costly retrofits. A cleanroom construction that anticipates growth will be more adaptable to changing production volumes, regulatory shifts, and process upgrades.
Establish a Contingency Plan
Even with detailed planning, unexpected issues can arise. From material shortages to weather delays, good cleanroom construction management includes contingency planning. Build some buffer time into your schedule and allocate budget for unforeseen expenses.
Some teams create tiered contingency plans based on project milestones, which makes it easier to adapt in real-time without pausing the entire project. Having a risk mitigation strategy in place helps maintain momentum and avoids stress during critical stages of the build.
Long-Term Maintenance Should Be Part of the Plan
Cleanroom success doesn’t stop at construction. Long-term performance depends on proper maintenance of your HVAC system, cleanroom surfaces, and equipment.
Working with your contractor or cleanroom builder to establish a maintenance plan early on sets you up for operational success. Document filter replacement schedules, pressure checks, and airflow monitoring routines before turnover.
Also, ensure your cleanroom construction includes access panels and serviceable layouts so maintenance doesn’t disrupt production. Ongoing monitoring, scheduled cleaning, and consistent inspections are necessary to retain your cleanroom classification over time.

How DesignTek Consulting Supports Cleanroom Success
At DesignTek Consulting, we know that successful cleanroom construction starts with the right strategy and ends with exceptional execution. Our team brings deep experience in cleanroom design, cleanroom HVAC, and construction management to ensure your cleanroom performs from day one. We work closely with clients across industries to deliver precision-built clean rooms that meet regulatory standards without disrupting operational goals.
Ready to take the stress out of cleanroom construction? Contact DesignTek Consulting to learn how our cleanroom construction management services can support your next project—from planning to performance. Take a look at all of the other services we offer on our website.
Comentarios