Cleanrooms are vital across various industries, from pharmaceuticals to electronics manufacturing. They provide a controlled environment where contaminants, temperature, humidity, and airflow are regulated to meet specific standards. When building a cleanroom, organizations often face a significant decision: Should they opt for a modular or traditional cleanroom? Understanding the differences, benefits, and limitations of each can help make an informed choice.
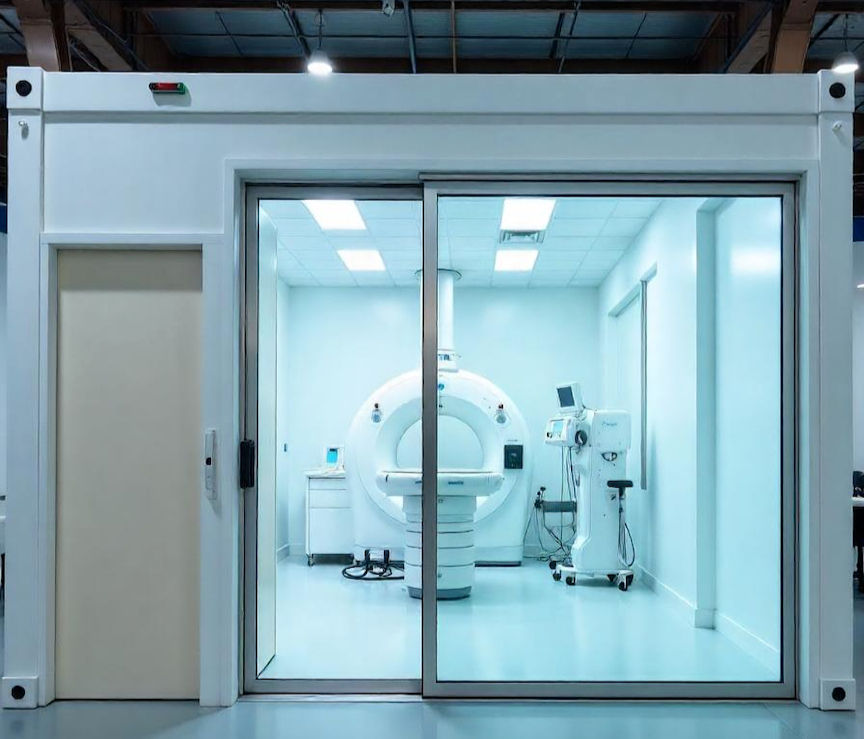
Understanding Modular vs Traditional Cleanrooms
What is a Modular Cleanroom?
Modular cleanrooms are prefabricated systems designed to be quickly assembled on-site. These cleanrooms use standardized components, making them adaptable to various spaces and requirements. They are ideal for companies seeking flexibility, quick installation, and scalability. Modular cleanrooms are often used in industries that require a rapid response to market changes or evolving production demands. With modular systems, companies can integrate features like advanced air filtration systems and cleanroom HVAC without extensive downtime.
What is a Traditional Cleanroom?
Traditional cleanrooms are built using conventional construction methods. They are typically integrated into the facility's architecture, offering long-term solutions with extensive customization options. Though they take longer to construct, traditional cleanrooms are often preferred for complex, large-scale operations that demand durability, long-term stability, and precise environmental control. These cleanrooms are suited for permanent installations where frequent modifications are not anticipated.
Key Differences Between Modular and Traditional Cleanrooms
1. Installation Time
Modular Cleanrooms: Installation is quicker, often completed in weeks. Prefabricated components streamline the process, minimizing disruption to existing operations. Rapid deployment makes modular systems ideal for companies under strict production timelines or compliance deadlines. In the context of modular vs traditional cleanrooms, installation speed is a significant advantage for modular options.
Traditional Cleanrooms: Construction can take several months. The process involves detailed planning, permits, construction management, and integration with existing infrastructure. While the extended timeline allows for greater customization, it may not be suitable for facilities requiring immediate operational readiness.
2. Flexibility and Scalability
Modular Cleanrooms: Easily modified, expanded, or relocated to meet changing operational needs. Industries like biotechnology, pharmaceuticals, and electronics manufacturing benefit from this flexibility. Modular solutions accommodate future technological upgrades without significant reconstruction. The modular vs traditional cleanrooms debate often centers around this adaptability, with modular solutions providing unmatched versatility.
Traditional Cleanrooms: Modifications are costly and time-consuming. Scaling operations may require substantial renovations, impacting production schedules and increasing costs. Facilities that prioritize long-term stability over adaptability often favor traditional cleanrooms.
3. Cost Considerations
Modular Cleanrooms: Lower initial costs and faster installation translate to quicker returns on investment. They are suitable for companies with budget constraints, short-term projects, or temporary operations. Additionally, modular cleanrooms can help reduce operational downtime, indirectly saving costs.
Traditional Cleanrooms: Higher upfront costs but often more cost-effective in the long term for permanent installations. Custom design options and durable materials can justify the initial investment for organizations seeking longevity and minimal maintenance.
4. Compliance and Certification
Both modular and traditional cleanrooms must meet strict cleanroom classification standards, ensuring they provide a controlled environment that minimizes contaminants. Modular systems often arrive pre-engineered to comply with cleanroom certification requirements, streamlining the validation process. Traditional cleanrooms may require more comprehensive documentation and testing to achieve compliance.
Advantages of Modular Cleanrooms
Speedy Construction
With prefabricated components, modular cleanrooms offer a faster solution, which is crucial for industries needing quick operational readiness. Companies can often transition to full production within weeks rather than months.
Flexibility
Modular systems are easy to reconfigure, relocate, or expand, making them ideal for businesses experiencing growth or changes in production requirements. This flexibility enables companies to stay competitive in rapidly evolving markets.
Cost Savings
Reduced installation time and lower material costs make modular cleanrooms a cost-effective choice. Businesses can allocate savings toward other operational needs or technological advancements.
Minimal Disruption
Since most components are built off-site, installation causes less interference with existing operations, allowing facilities to continue production during construction.

Advantages of Traditional Cleanrooms
Long-Term Durability
Traditional cleanrooms are built to last, providing a robust and permanent solution. They are ideal for facilities that require high-level cleanliness and stability over extended periods.
Customization
These cleanrooms offer extensive customization options, catering to specific industry needs, including advanced HVAC systems, specialized air filtration systems, and complex workflows. Organizations in aerospace and semiconductor industries often require such custom features.
Integration with Facility Infrastructure
Traditional cleanrooms can be seamlessly integrated into the building's existing systems, including wastewater management, electrical systems, and utilities. This integration enhances operational efficiency and environmental control.
HVAC and Air Filtration Considerations
Importance of Cleanroom HVAC Systems
Whether modular or traditional, the cleanroom HVAC system plays a pivotal role in maintaining a controlled environment. Factors to consider include:
Air change rates to remove contaminants
Humidity control to prevent material degradation
Temperature stability for consistent production conditions
Advanced air filtration systems to achieve desired cleanliness levels
Both types of cleanrooms require specialized air filtration systems to maintain cleanliness standards according to cleanroom classification guidelines. High-efficiency particulate air (HEPA) and ultra-low penetration air (ULPA) filters are commonly used to meet regulatory standards.
Wastewater Management in Cleanroom Construction
Effective wastewater management is essential in industries like pharmaceuticals, semiconductor manufacturing, and biotechnology. Modular cleanrooms often feature built-in wastewater management systems that comply with environmental regulations. Traditional cleanrooms, while customizable, may require separate planning and infrastructure integration, potentially increasing project timelines and costs.
Maintenance and Lifecycle Costs
Modular Cleanrooms
Easier to maintain with replaceable panels and modular components.
Minimal downtime during repairs or upgrades.
Lower long-term maintenance costs.
Traditional Cleanrooms
Durable but may require extensive repairs over time.
Maintenance can be disruptive due to integrated systems.
Higher initial construction costs are offset by long-term stability.
Environmental Impact and Sustainability
Sustainability Considerations
Modular cleanrooms offer an eco-friendly alternative through reduced construction waste, recyclable components, and energy-efficient designs. Companies seeking to achieve sustainability goals may prefer modular systems. Traditional cleanrooms, while durable, often consume more resources during construction and require more extensive material use.
Selecting the Right Cleanroom Contractor
Working with an experienced cleanroom contractor is crucial to the success of your project. An expert cleanroom builder ensures:
Accurate cleanroom design tailored to operational needs.
Compliance with cleanroom classification standards.
Efficient construction management to meet deadlines and budgets.
Industry Applications for Modular vs Traditional Cleanrooms
Pharmaceuticals and Biotechnology
Modular cleanrooms provide flexibility for changing research protocols.
Traditional cleanrooms meet stringent regulatory standards for large-scale production.
Semiconductor and Electronics Manufacturing
High-level cleanroom classifications often require traditional cleanrooms.
Modular systems can be used for R&D or pilot production lines.
Aerospace and Defense
Traditional cleanrooms ensure long-term durability and precise environmental control.
Medical Device Manufacturing
Both cleanroom types can meet regulatory requirements depending on production scale and flexibility needs.
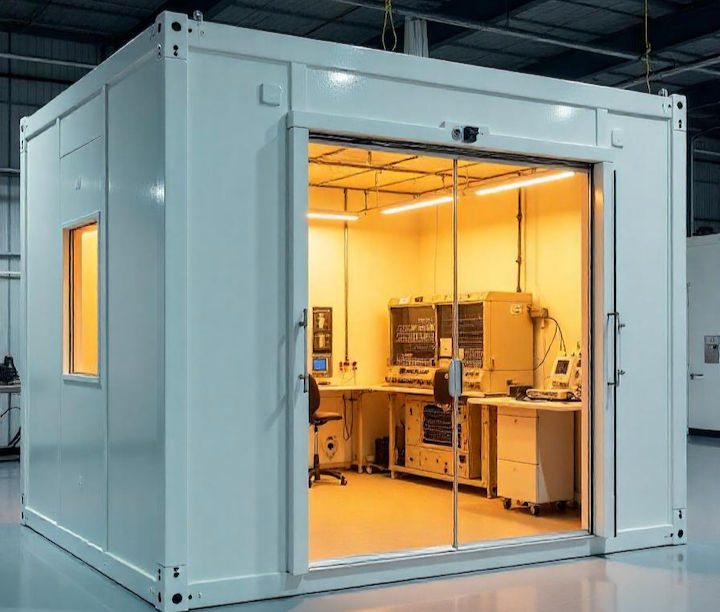
How DesignTek Consulting Can Help
At DesignTek Consulting, we understand the complexities of choosing the right cleanroom services. Whether you’re considering a modular or traditional design, our team provides end-to-end support in cleanroom design, construction management, and cleanroom certification to ensure you meet your operational goals efficiently and cost-effectively. We work closely with clients to deliver cleanrooms that meet cleanroom classification standards while optimizing functionality and cost-efficiency.
Ready to explore the best cleanroom solution for your facility? Contact DesignTek Consulting to discuss your needs and discover how we can help you create a cleanroom that meets your specifications and budget.
Comments