The Challenges of a USP 797 Pharmaceutical Cleanroom
- Preston Grimes
- Oct 27, 2016
- 2 min read
Updated: Apr 28, 2024
A pharmaceutical cleanroom must meet established federal standards to ensure that its design and construction result in a properly sterile environment. Although the reasons for these rigorous standards are complex, the ultimate goal is the protection of public health and safety. The regulation that dictates cleanroom standards, issued by the United States Pharmacopeia, is known as USP 797, although relevant guidelines are in USP 800 also. Compliance with the USP standards is mandatory for any company that works with compounding sterile preparation of pharmaceutical products.
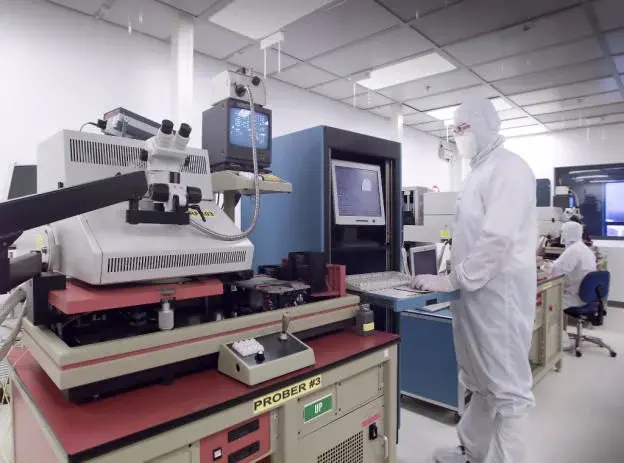
Why Standards Are Necessary The U.S. Food and Drug Administration (FDA) advises in Title 21 of the Code of Federal Regulations, that protecting the sterile nature of any location where pharmaceutical products are handled is the most effective means of protecting the public, as well as healthcare and pharmaceutical professionals.
Pharmaceutical compounding is the practice of mixing ingredients to meet specific goals. Although this was used originally by individual pharmacists to create patient-specific medications, it is used today on a large-scale basis in the process of manufacturing drugs.
Using a minimum standard cleanroom environment for this process ensures the purity of compounded pharmaceuticals, but that’s only part of the reason for the regulation. USP 797 standards also protect those personnel who handle potentially hazardous products from unwanted contamination, a significant risk posed today by many pharmaceutical ingredients.
USP 797 and USP 800 Guidelines The USP, a nonprofit government agency, oversees safety standards for all prescription and over-the-counter drugs. In 2004, the USP issued the first guidelines addressing the sterile requirements for those facilities that mix, handle or transport compound pharmaceutical products.
The standards have been modified and upgraded several times since, to keep pace with new developments in technology. The standards dictate both the facilities’ design and use.
Companies must evaluate the risk of their compounding activities and develop an action plan for compliance. Actions plans must address employee training, cleaning procedures, waste disposal and the methods and supplies that may be used.
The United States Pharmacopeia currently plant to update the USP 797 standards in late 2016. USP 800, issued in 2015, builds upon USP 797 and related standards, to provide an expanded level of consumer protection.
Ways to Ensure USP Compliance In the design and planning stages of a USP 797 cleanroom, clients work with an industrial or cleanroom engineer to determine the required specifications.
Depending on the level of risk (low, medium or high) posed by the materials that will be used, the facility will require a biological safety cabinet for compounding and a specific fume hood design. These are then situated inside a larger buffer zone, a positive pressure-controlled environment (cleanroom).
The most effective way to ensure compliance with current standards is to work with an engineering firm who understands current USP regulations and the design specifications they require.
DesignTek Consulting Group is Salt Lake City’s expert engineering and engineering consulting firm. Our engineers, designers, project managers and technical staff have extensive training and experience with industrial, pharmaceutical cleanroom design and construction.
Contact DesignTek today to learn more about our expertise in pharmaceutical cleanroom design and consultation.
Comentarios