The Role of HVAC in Cleanroom Compliance
- zachsievert15
- 1 hour ago
- 5 min read
Maintaining compliance in cleanrooms goes far beyond just controlling dust or wiping down surfaces. At the heart of cleanroom performance is something you can’t always see but definitely feel—the HVAC system. When done right, HVAC in cleanroom compliance ensures a controlled environment that supports safety, product integrity, and regulatory standards.
Whether you're designing a new cleanroom, retrofitting an existing facility, or improving air handling to meet certification requirements, the HVAC system plays a pivotal role in ensuring your cleanroom functions properly and stays within the necessary cleanroom classification. Let's explore why that is, what goes into a compliant HVAC system, and how each piece connects with broader cleanroom operations.
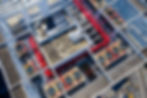
Table of Contents
Why HVAC in Cleanroom Compliance Matters
Key Elements of a Compliant Cleanroom HVAC System
The HVAC System’s Role in Regulatory Compliance
Planning and Engineering for HVAC Success
Common HVAC Mistakes That Can Lead to Non-Compliance
How Cleanroom HVAC Interacts with Other Critical Systems
Cleanroom Compliance Starts with Smart HVAC Design
How DesignTek Consulting Supports HVAC in Cleanroom Compliance
Why HVAC in Cleanroom Compliance Matters
Cleanrooms are used in industries where even microscopic particles can interfere with production. Think pharmaceuticals, semiconductors, biotechnology, and medical devices. Any lapse in air control can lead to contamination, failed batches, or worse—regulatory fines and product recalls.
This is where HVAC in cleanroom compliance comes into play. The HVAC system isn't just about keeping the space comfortable. It's responsible for controlling temperature, humidity, airflow, and—most importantly—particulate levels through advanced air filtration systems. These conditions are essential for meeting ISO standards and GMP requirements, which are non-negotiable in regulated industries.
Key Elements of a Compliant Cleanroom HVAC System
Temperature and Humidity Control
The HVAC system must maintain a consistent temperature and relative humidity level to meet environmental specifications. Depending on your cleanroom class and industry, the acceptable range can be tight. Too much humidity can encourage microbial growth, while low humidity can lead to static discharge—both of which are threats in sensitive environments.
Pressure Differentials
Cleanrooms often use positive or negative pressure, depending on their function. A positively pressured cleanroom pushes air out when doors open, keeping contaminants from entering. This is ideal for pharmaceutical or microelectronics environments. Negative pressure, on the other hand, is used when working with hazardous materials, keeping contaminants from escaping the room.
Maintaining stable pressure differentials is a job that falls squarely on the HVAC system, which must be engineered to maintain those levels consistently—even with people, equipment, and door usage factored in.
Air Changes Per Hour (ACPH)
A major factor in cleanroom design and compliance is air changes per hour. This refers to how frequently the total volume of air in the room is replaced. A higher ACPH means more filtered air is circulating, reducing the risk of particle buildup. Depending on cleanroom classification, this could range from 20 to over 400 air changes per hour.
Achieving and maintaining these air changes depends on a well-calibrated HVAC system paired with the right HEPA or ULPA filters.
Filtration Systems
No HVAC discussion is complete without focusing on air filtration systems. HEPA filters (High-Efficiency Particulate Air) are typically used in Class 1000 or higher cleanrooms, while ULPA filters (Ultra-Low Penetration Air) are found in even stricter classifications like Class 100 or Class 10 cleanrooms.
These filters remove particles down to 0.3 microns or smaller, and are a cornerstone of cleanroom compliance. However, filters are only as effective as the HVAC system supporting them. Airflow velocity, filter placement, and room layout all factor into how well particles are captured and prevented from circulating.
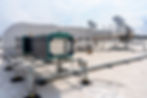
The HVAC System’s Role in Regulatory Compliance
Cleanrooms must meet standards such as ISO 14644, USP <797>, or FDA 21 CFR Part 11, depending on the industry. These regulations spell out detailed environmental requirements, including particulate limits, air change rates, temperature ranges, and more.
A cleanroom HVAC system must be engineered to consistently meet these requirements, and its performance is often verified through routine environmental monitoring and recertification processes. Any fluctuation in system performance—like a clogged filter, a mis-balanced damper, or poor pressure regulation—can push the cleanroom out of spec and trigger compliance issues.
That’s why cleanroom HVAC systems are often built with redundancies and alarms, allowing for real-time monitoring and rapid response if conditions drift from the required thresholds.
Planning and Engineering for HVAC Success
Start with the Right Cleanroom Design
Compliance starts early in the planning process. The layout, number of rooms, entry points, and even equipment placement all influence HVAC load and airflow patterns. Collaborating with an experienced cleanroom builder or cleanroom contractor from the beginning helps avoid costly redesigns down the line.
DesignTek Consulting works with clients to plan cleanroom engineering solutions that take HVAC system demands into account from the start, ensuring long-term compliance and functionality.
Choose Experienced Partners
HVAC in cleanroom compliance is complex and highly technical. Not every HVAC system is suited for this environment, and not every HVAC contractor understands the precision required. A qualified cleanroom contractor or engineering team understands how to balance mechanical systems, airflow patterns, filtration, and room pressurization based on cleanroom classification needs.
Don’t Forget About Construction Management
During cleanroom construction, keeping dust, debris, and unfiltered airflow under control is critical. A single mistake during installation—such as leaving filter grilles uncovered or failing to isolate the ductwork—can compromise the clean room before it even begins operation.
A strong construction management process ensures that HVAC components are installed to spec, leak-tested, and verified before cleanroom commissioning.
Common HVAC Mistakes That Can Lead to Non-Compliance
Even small missteps in HVAC performance can cause compliance issues. Here are a few examples to watch for:
Improper filter maintenance:Â Clogged filters reduce airflow and throw off pressure balances.
Unbalanced airflows:Â Too much supply air without proper exhaust can create turbulence, allowing particles to linger.
Inadequate monitoring systems:Â Without real-time data, issues can go undetected until inspections or audits.
Lack of redundancy:Â Single-point failures in temperature or pressure control can take an entire cleanroom offline.
Addressing these risks requires more than just solid HVAC equipment—it takes ongoing attention, preventive maintenance, and smart cleanroom engineering from the start.
How Cleanroom HVAC Interacts with Other Critical Systems
HVAC systems don’t operate in isolation. They interact closely with other cleanroom systems such as:
Cleanroom design and layout
Airlocks and pass-throughs
Cleanroom construction materials
Wastewater management systems
Process equipment with heat loads
Each of these components affects the HVAC system’s workload and performance. For example, cleanrooms with large heat-generating equipment may require additional cooling capacity, while operations that generate moisture call for enhanced humidity control. Coordination across all systems is essential to avoid cross-contamination or system overloads.
Cleanroom Compliance Starts with Smart HVAC Design
HVAC systems form the backbone of cleanroom compliance. From maintaining air cleanliness and pressure differentials to supporting strict environmental controls, the role of HVAC in cleanroom compliance is critical and non-negotiable. Whether you're working in pharmaceutical manufacturing, electronics, or biomedical research, your cleanroom’s success—and your regulatory standing—depends on it.
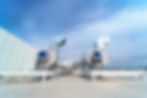
How DesignTek Consulting Supports HVAC in Cleanroom Compliance
At DesignTek Consulting, cleanroom HVAC isn’t an afterthought—it’s a priority. Our team of experienced professionals delivers comprehensive cleanroom engineering services that account for every aspect of compliance, from air filtration systems and airflow patterns to construction management and HVAC system integration. Check out the wide variety of services we can offer your business.
Whether you're building from the ground up or optimizing an existing facility, we help create cleanrooms that work as hard as you do. Contact us to learn how we can support your cleanroom project with expert HVAC solutions built for lasting compliance.