Why Industry-Specific Cleanroom Design Matters
- zachsievert15
- Nov 12, 2024
- 4 min read
In many specialized industries, cleanrooms are essential environments that enable safe, contamination-free operations. Cleanroom design is a complex process that goes beyond simply setting up a sterile space; it requires a tailored approach for each industry to meet unique regulatory standards, operational needs, and environmental control requirements. By focusing on industry-specific cleanroom design, companies ensure that their facilities not only maintain cleanliness but also achieve optimal functionality. This article explores why industry-specific cleanroom design is so important and what it entails, highlighting the advantages it brings to various sectors.

What Is Industry-Specific Cleanroom Design?
Industry-specific cleanroom design involves creating a controlled environment that meets the distinct needs of different industries, whether pharmaceutical, electronics, aerospace, or biotech. Each of these industries has stringent requirements for maintaining low levels of particulates, airborne organisms, and other contaminants. For example, a cleanroom used for microelectronics manufacturing will have different requirements than one used in biopharmaceutical production. Industry-specific design tailors each cleanroom's specifications—such as airflow, temperature, humidity, and pressure—to comply with the exact needs of a particular industry and its regulatory guidelines. This tailored approach helps companies avoid costly errors and achieve optimal performance in their cleanrooms.
Key Components of Cleanroom Design
The basics of cleanroom design revolve around several key components that contribute to effective contamination control. These include:
Airflow and Filtration: The HVAC system in a cleanroom is crucial, as it regulates airflow to remove contaminants and maintain cleanroom certification standards. High-efficiency particulate air (HEPA) filters or even ultra-low penetration air (ULPA) filters are often used to filter out particulates. Cleanroom HVAC systems are engineered for high-performance filtering while maintaining desired temperature and humidity levels.
Controlled Pressure Levels: Different areas within a cleanroom may require varied pressure levels to prevent cross-contamination. Positive pressure environments are typically used to keep contaminants out, whereas negative pressure environments might be necessary to contain certain materials, such as hazardous chemicals or sensitive bio-products.
Temperature and Humidity Control: Each industry has specific needs for temperature and humidity that help maintain product integrity and safety. An electronics cleanroom, for example, may have lower humidity requirements to prevent static discharge, while a pharmaceutical cleanroom needs precise humidity control to prevent contamination and ensure product efficacy.
Wastewater Management: In industries such as pharmaceuticals or biotech, the cleanroom design may include wastewater management systems to handle chemical waste or byproducts generated during production. This helps keep the environment controlled and compliant with environmental regulations, making it safer for both products and workers.
These elements are adjusted and optimized based on the industry's requirements to achieve the most effective cleanroom design. Each aspect works in tandem to create an environment free from unwanted contaminants and conducive to high-quality production.
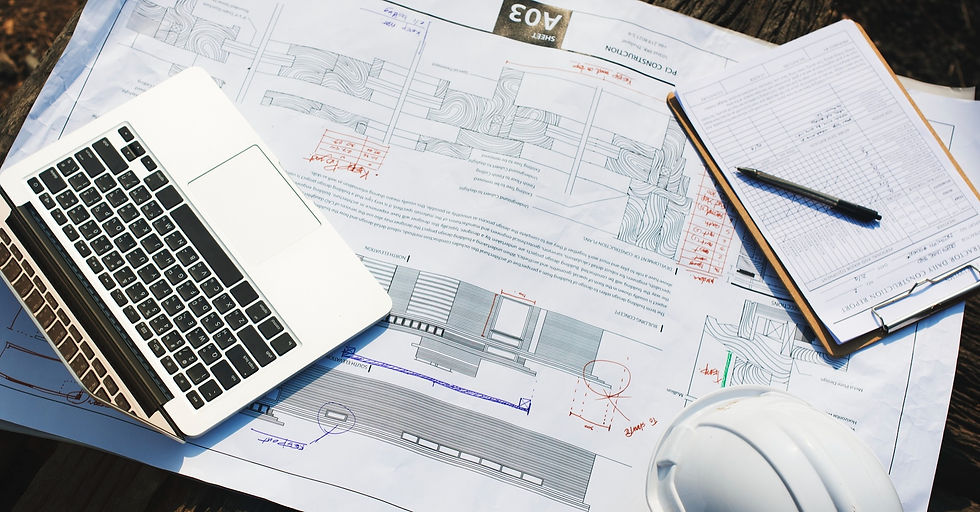
The Role of Regulations in Cleanroom Design
Regulatory compliance is a major reason industry-specific cleanroom design is necessary. Organizations such as the Food and Drug Administration (FDA) in the United States and the European Medicines Agency (EMA) in Europe enforce stringent guidelines on cleanroom construction and operation, particularly in healthcare, biotech, and pharmaceutical sectors. Cleanroom engineers work closely with clients to develop designs that meet these compliance standards, which cover various factors like particulate control, microbial limits, and airflow quality.
Without the proper certification, cleanrooms may not be legally approved for operation, leading to setbacks and costly redesigns. A cleanroom builder familiar with industry regulations ensures that every aspect of the cleanroom—from flooring materials to HVAC system requirements—meets these standards. Following these guidelines also helps avoid fines, ensuring operations remain uninterrupted.
Importance of Industry-Specific Cleanroom Construction
In addition to design, construction of a cleanroom requires specialized expertise. Cleanroom construction management involves coordinating a team of cleanroom contractors, HVAC specialists, and engineers to bring the design to life. Every part of the build—from the materials used to the construction methods applied—must work toward maintaining the cleanroom’s integrity. Inadequate cleanroom construction can lead to compromised control over environmental conditions, resulting in costly repairs or operational inefficiencies.
For example, in the microelectronics industry, even a single particle can lead to product failure. In such cases, the cleanroom construction must emphasize highly sensitive filtration and isolation techniques. Meanwhile, in the life sciences, the emphasis may be on microbial control, requiring precise airflow management and specialized surfaces that reduce microbial growth. A successful cleanroom build is one where the construction aligns seamlessly with the specific needs of the industry and upholds the highest quality standards.
How Cleanroom Engineering Impacts Performance and Safety
The engineering behind a cleanroom doesn’t just affect functionality; it can also impact operational safety and efficiency. Cleanroom engineers are tasked with ensuring the space meets rigorous standards for both personnel safety and product integrity. In sectors like aerospace or healthcare, where the stakes are high, specialized cleanroom engineering is critical. Engineers factor in ergonomic layouts, emergency protocols, and efficient workflows to support not only contamination control but also safe working conditions.
When cleanrooms are engineered to account for both safety and specific operational needs, they significantly improve both performance and longevity, protecting both the products and the people involved. This thorough engineering also helps avoid costly downtime by keeping systems functioning at peak efficiency.
HVAC System Considerations in Cleanroom Design
The HVAC system is a core element of cleanroom functionality. In industry-specific cleanroom design, the HVAC requirements vary depending on what the space will be used for. A cleanroom HVAC system must handle extensive filtration and maintain stable temperature and humidity levels. Cleanroom HVAC requirements are often much more stringent than those in standard buildings, given that they serve as the primary method of controlling contaminants.
For instance, semiconductor manufacturing facilities might need extremely low particulate levels, calling for a robust HVAC system that can handle high rates of air exchange and maintain cleanroom certification standards. A dedicated cleanroom HVAC system can also help lower operational costs by improving energy efficiency while ensuring cleanroom conditions remain stable over time.

Cleanroom Design Tailored to Your Industry with DesignTek Consulting
Working with an experienced cleanroom contractor can streamline the entire process of designing and constructing an industry-specific cleanroom. At DesignTek Consulting, our team specializes in crafting cleanroom solutions tailored to meet the unique challenges of your industry. From initial design to cleanroom construction management and ongoing support, we offer comprehensive solutions that ensure your cleanroom performs optimally and remains compliant with all relevant standards. Check out our services to see how DesignTek can help with your build.
If you're ready to start on your cleanroom project, visit our website or contact us today to see how our expertise can make a difference in your cleanroom’s quality, efficiency, and safety.
Comments